Noticias
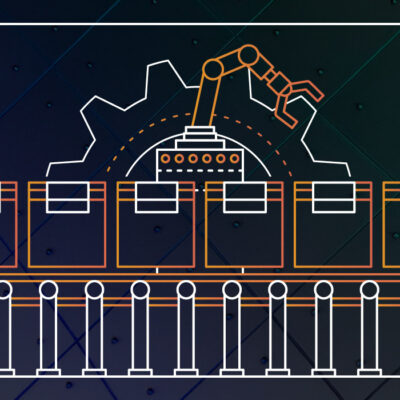
12 consideraciones de diseño de implementación por lotes
Los sistemas por lotes se utilizan para maximizar el control de calidad, minimizar costos y reducir pérdidas al fabricar lotes más pequeños en comparación con un modelo de producción en masa, razón por la cual las empresas de las industrias de alimentos y bebidas, farmacéutica y química confían en ellos. El público objetivo de un sistema por lotes es variado y, por lo tanto, la implementación adecuada de un sistema por lotes debe considerar muchos factores. Desde el Gerente de Planta, Operaciones, Ingeniería y Mantenimiento hasta los Operadores, todas estas personas tienen necesidades únicas que deben considerarse.
Las mejores prácticas establecidas por estándares como ISA 88 e ISA 95 proporcionan una excelente guía o punto de partida, pero estos estándares no prescriben cómo implementar los detalles de una solución. Por lo tanto, lo siguiente pretende resaltar algunas de las consideraciones para el diseño de un sistema.
CREACIÓN DE UN MODELO DE EQUIPO ROBUSTO PARA UN RENDIMIENTO ÓPTIMO DE LA PLANTA
Las capacidades de una planta sobre qué productos y cómo se pueden fabricar allí residen en las capacidades de sus equipos, materiales y personal. Estas capacidades son capturadas por el modelo de equipo como se define en ISA 88 y 95. Una vez que captura estas capacidades, se exponen al autor de la receta para definir cómo ejecutar el flujo de trabajo de fabricación del producto, que se detalla en el modelo de procedimiento ISA 88.
Tener un modelo de equipo bien definido es fundamental para permitir las máximas capacidades de la planta y al mismo tiempo brindar al autor de recetas y a los operadores una experiencia intuitiva. La definición de capacidades del equipo debe incluir las actividades que el sistema de control de automatización puede realizar (por ejemplo, agregar agua), así como las actividades realizadas por los operadores y otro personal (por ejemplo, adiciones manuales, datos de muestras de laboratorio, etc.).
PASOS SUGERIDOS PARA DISEÑAR UN SISTEMA POR LOTES
Los diagramas de proceso e instrumentación (P&IDs) pueden definir muchas capacidades, pero otras capacidades no aparecerán en estos documentos. Puede definirlos entendiendo cuáles pueden ser las actividades del operador. El siguiente enfoque me ha servido para centrarme metódicamente en las diferentes consideraciones de diseño:
Paso 1: comprender el alcance del proyecto.
En el ámbito vertical, ¿la solución recibirá pedidos de un sistema ERP? ¿O el operador iniciará una receta de control y la pondrá en marcha? En el ámbito horizontal, ¿incluye la recepción y gestión de la materia prima hasta el almacenamiento, embalaje o envío del producto terminado?
Paso 2: Identificar las celdas y unidades del proceso.
Al definir el modelo de equipo ISA 88, es necesario identificar las celdas y unidades del proceso. Para determinar qué unidades existen, debemos tener en cuenta que las recetas según el Modelo de Procedimiento o flujos de trabajo ISA 88 se ejecutan contra una unidad, como un recipiente de pesaje previo, mezclador, reactor, cocedor, licuador, fermentador o similar.
Otras ubicaciones donde es posible que sea necesario especificar los flujos de trabajo mediante instrucciones pueden ser áreas de pesaje previo manual de ingredientes menores y micro, áreas de recepción y envío de materiales, etc. Tenga en cuenta que una unidad no debe tener la forma física de un recipiente y que no todos los recipientes son unidades. Es posible que en el diseño se incluyan equipos que deban limpiarse o esterilizarse por separado de los principales recipientes de procesamiento, como líneas de transferencia.
Paso 3: Enfocarse en las fases de ISA 88 en cada unidad.
Una vez identificadas las unidades, céntrese en las fases de ISA 88 pertenecientes a cada unidad. Tenga en cuenta que es mejor centrarse en las acciones (verbos) y no en los detalles de la fase en este momento (es decir, qué parámetros utiliza, qué información capturará para generar informes, etc.). No nos centramos en qué equipo se utilizará para realizar cada acción, teniendo en cuenta también que las definiciones de los nombres de las fases son las que presentará al autor de la receta para construir las recetas que especifican el flujo de trabajo.
En este paso, solo nos centraremos en el flujo de material que ingresa al equipo del proceso de fabricación, cómo se transfiere entre unidades y cómo se elimina del proceso de fabricación. Por ejemplo, podemos identificar estas fases como recepción del camión, adición de material, adición manual de material, transferencia de salida desde una unidad, transferencia de entrada, descarga al almacenamiento, transferencia al embalaje, carga del camión, etc.
Paso 4: Enfocarse en las fases dentro de la unidad.
A continuación, nos centraremos en qué fases existen dentro de la unidad. Las fases comunes son agitación o mezcla, control de calor, enfriamiento o temperatura, control de presión, verificación de la preparación del equipo, verificación del estado de limpieza del equipo, limpieza en el lugar o indicaciones del operador como tomar una muestra, preparar el equipo, etc.
Paso 5: Identificar la información de la unidad que puede utilizar para determinar las condiciones de transición de la receta.
Ejemplos de información unitaria que se puede utilizar para determinar las condiciones de transición de la receta incluyen el peso del recipiente, el nivel, la presión, la temperatura, el pH u otra información del instrumento. El autor de la receta puede utilizar estos valores para tomar decisiones sobre la receta y definir cuándo debe comenzar o finalizar un paso.
Paso 6: Determinar el arbitraje de equipos.
En este paso, definimos qué equipo se utiliza para cada fase y determinamos qué fases se comparten entre varias unidades. Tenga en cuenta que un recurso puede ser compartido por más de una unidad o fase.
Paso 7: Definir los parámetros de la fase y la información a reportar.
En este paso, definimos la información relevante requerida para realizar la fase (verbo). Con esta información, podemos especificar claramente cómo realizar una fase (acción). Puede especificar la complejidad de una fase no solo para aplicar una acción crítica sino también para capturar cualquier información pertinente que ayudará a determinar cómo se ejecutó cada tarea. Tenga en cuenta que el autor de la receta especifica todos estos valores de etiqueta como información que termina en el registro del lote. Estas son algunas recomendaciones:
- Proporcione nombres significativos para que el autor de la receta y la información reportada puedan ser útiles, por ejemplo, punto de ajuste de cantidad, no solo punto de ajuste o simplemente cantidad.
- Mantener consistencia con la convención de nombres.
- Capture en un informe el valor y el número de instancias si el operador u otra lógica cambió algún parámetro especificado por la receta, por ejemplo, el punto de ajuste de la velocidad del agitador cambió.
- Las fases de adición de material notifican al operador si la adición está fuera de tolerancia y le permite seleccionar qué acción tomar.
- Las fases de adición de material aprenden el valor previo a la acción y actualizan instancias futuras de acuerdo con la compensación aprendida.
- Puede configurar las fases de dosificación de material para especificar el punto de ajuste de la cantidad para el ajuste dinámico de la cantidad según las propiedades del material, es decir, ajustar la cantidad de grano para compensar el contenido de humedad y actualizar aún más el punto de ajuste de la cantidad de agua requerida para tener en cuenta la cantidad de agua que ingreso con el grano.
- Cada fase que requiere el uso de equipo debe verificar el estado del equipo requerido y notificar al operador si las condiciones no son las requeridas, es decir, si algún equipo requerido tiene fallas o está en modo de operador.
Paso 8: Diseñar la fase de modo que el autor de la receta solo deba especificar valores de parámetros de fase básicos.
El autor de la receta especifica los valores de los parámetros de fase. Hay otros parámetros que requiere la fase que no deben estar en el parámetro de receta sino como un parámetro de ingeniería para realizar una tarea.
Los ejemplos incluyen los parámetros de ajuste de un circuito de control de temperatura o la cantidad de material previo a la acción que requiere una fase de dosificación o adición. Parte del diseño debe consistir en brindar al autor de la receta la capacidad de especificar cómo elaborar un producto sin requerir conocimientos detallados de cómo realizar esta tarea, es decir, agregar agua, simplemente especificando la cantidad de punto de ajuste requerido.
Paso 9: Crear valores de informe que proporcionen información adicional.
Por ejemplo, durante la adición de un material, normalmente se captura la cantidad real de material agregado, pero la fase también puede capturar el peso del recipiente antes de comenzar la adición y después de completarla.
Puede utilizar este tipo de información para realizar investigaciones. Por ejemplo, si sabemos cuál era el peso del tanque al final de la dosificación del Material A pero, durante la adición del Material B, el peso inicial no coincidió con el final del Material A, puede que haya algo que valga la pena analizar.
Paso 10: Utilizar los valores del informe para obtener conocimientos sobre su proceso y producto.
Los valores de informe adicionales pueden incluir cosas como máximos y mínimos para caudales, temperaturas, velocidades, torque, etc. Puede utilizar esta información para comprender mejor el desempeño del proceso y su impacto en la calidad o el rendimiento del producto.
Paso 11: Proporcionar parámetros adicionales al autor de la receta.
Dado que nosotros, los ingenieros, no sabemos qué acción de procedimiento desea el autor de la receta durante una excepción de ejecución, debemos proporcionar parámetros adicionales para darle al autor la capacidad de determinar el comportamiento correctivo.
Por ejemplo, si una receta se pone en espera o se pone en pausa, ¿qué debería pasar con el punto de ajuste de velocidad del agitador, el punto de ajuste de temperatura o el comportamiento de un temporizador? ¿Debería continuar o no? El comportamiento de retención podría ser continuar, mantener el valor o restablecer, etc. Para esto, proporcionamos parámetros adicionales como el punto de ajuste de velocidad de retención, el punto de configuración de temperatura de retención o el modo de temporizador.
Paso 12: Verificar el estado de tu equipo.
Otras fases pueden incluir una fase utilizada al inicio de una receta que verifica el estado de todo el equipo de esa unidad. Luego, esta fase notificará al operador si algún equipo de la unidad no está listo para ser utilizado, por lo que el operador puede decidir continuar o resolver el problema antes de que comiencen las actividades de la unidad.
Otros ejemplos pueden incluir fases que puede utilizar para sincronizar actividades entre unidades, aquellas que realizan un seguimiento y actualizan el estado de limpieza de una unidad y fases que informan visualmente al operador a través de la HMI de las actividades actuales que tienen lugar en la unidad.
Posted In: Bakery Industry, Blogs, Chemical Industry, Consumer Goods, Distilleries, Food Industry, Life Science Industry, Metals Industry, News